
Top 10 Benefits of a Quality Management System.
- 1. Increase Efficiency.
- 2. Increase Profitability.
- 3. Improve Employee Morale.
- 4. Improve Decision Making.
- 5. Improve Supplier & Vendor Relationships.
- greater efficiency and less waste.
- better and consistent control of major business processes.
- a better understanding of customer needs.
- regulation of successful working practices.
- improved risk management.
- increased customer satisfaction.
- improved participation of employees.
What are the advantages and disadvantages of quality management?
Total Quality Management : Advantages, Disadvantages, And Benefit
- Reduce the problem of the product or service
- Increased attention to customers
- Customer satisfaction increases
What is the importance of quality management?
- Abstract. ...
- Introduction. ...
- Materials and methods. ...
- Results and discussion. ...
- Conclusions. ...
- Acknowledgements. ...
- Funding. ...
- Author information. ...
- Ethics declarations. ...
- Additional information. ...
What is Total Quality Management and why is it important?
Your answer should explain the chosen principle and why/how it relates to what is being discussed.
- An ice cream shop owner notices that over the past few months, the number of people who order the rocky road ice cream has been declining. ...
- Your boss decides to put together a team to try to come up with ways to make better use of new technology to make your product faster.
- You work for a firm that sells pharmaceuticals. ...
What are the objectives of Total Quality Management?
What are the principles of TQM?
- Customer focus. Central to all successful TQM systems is an understanding that quality is determined by the customer. …
- Employee involvement. …
- Centred on process. …
- Integrated system. …
- Strategic & systematic approach. …
- Decision-making based on facts. …
- Communication. …
- Continuous improvement.
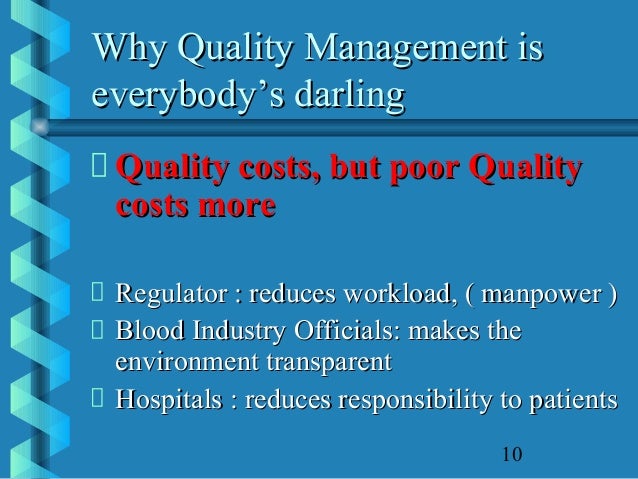
What is the purpose of quality management?
A quality management system (QMS) can be defined as a collection of business processes that focus on meeting customer requirements on a consistent basis. Its purpose is to ensure that, every time a process is performed, the same information, methods, skills and controls are used and applied in a consistent manner.
What are the benefits of quality system training?
Here are all the benefits of undergoing a quality management system training program: Increased efficiency: Business who go through quality management system training has the aim to maximise the efficiency and quality of their processes. ... Better Morale: ... International recognition: ... Process Improvement:
What are the objectives and benefits of quality management system documentation?
A QMS helps to coordinate and direct an organization's activities to meet customer and regulatory requirements and continually improve its effectiveness and efficiency. The QMS documentation must accurately and succinctly document the organisation's structure, procedures, processes and resources.
What are the benefits of quality?
Benefits of Total Quality ManagementStrengthened competitive position.Adaptability to changing or emerging market conditions and to environmental and other government regulations.Higher productivity.Enhanced market image.Elimination of defects and waste.Reduced costs and better cost management.Higher profitability.More items...
What are the internal benefits of quality management system?
Advantages of ISO 9001 better and consistent control of major business processes. a better understanding of customer needs. regulation of successful working practices. improved risk management.
What will be the benefits of implementing and integrating a quality management system on an organization?
An Integrated Management System (or “IMS”) can benefit your organization through increased efficiency and effectiveness, and cost reductions while minimizing the disruption caused by several external audits.
Why is there a need to have quality and how we are benefited from it?
Quality is critical to satisfying your customers and retaining their loyalty so they continue to buy from you in the future. Quality products make an important contribution to long-term revenue and profitability. They also enable you to charge and maintain higher prices.
What are the 7 quality management principles?
The seven principles of quality management are:Engagement of people.Customer focus.Leadership.Process approach.Improvement.Evidence-based decision making.Relationship management.
How does a quality management system affect an organization?
Benefits of a documented quality management system include: Meeting the customer’s requirements, which helps to instill confidence in the organization, in turn leading to more customers, more sales, and more repeat business.
What is QMS in business?
QMS - What are the Benefits of Quality Management Systems. A quality management system (QMS) is defined as a formalized system that documents processes, procedures, and responsibilities for achieving quality policies and objectives. A QMS helps coordinate and direct an organization’s activities to meet customer and regulatory requirements ...
What is ISO 9001:2015?
ISO 9001:2015 is the most recognized and implemented quality management system standard in the world. It specifies the requirements for a QMS that organizations can use to develop their own programs. Other standards related to quality management systems include the rest of the ISO 9000 family (ISO 9000 and ISO 9004).
How does TQM help employees?
TQM enables to bring changes in the behavioral pattern of the employees by facilitating good work culture, team-work, promoting self-development, employee engagement and thus extracting better performance.
Why is TQM important?
The increasing competition challenges the organization to meet the ever-increasing demands of the consumer market. TQM practices prove useful in understanding the market trends and competition so as to develop effective strategies to overcome the same.
What is TQM research?
TQM enables the organizations to conduct research on any undergoing challenges/ problems so as to come up with solutions for the same. Thus, organizations escalate their research and bring in innovative marketing decisions. The implemented innovative approach to the core and peripheral services attracts the customers.
What is the main focus of TQM?
Since the main focus of TQM is on customer satisfaction , it provides a pathway to understand the needs and demands of the consumer market. Therefore, it enables the organization to deliver products/services specific to the market.
What are the intangible returns of TQM?
But, also, intangible returns like better communication, teamwork, employee engagement, customer satisfaction, goodwill, and increased employee morale. However, TQM also requires employees to undergo a substantial duration of the training period, company-wide involvement and participation to quality improvement.
What is TQM in business?
As TQM focuses on consistent delivery of good quality product/services, the consumers hold favorable reputation about the organization. The internal stakeholders (employees and investors) get lucrative incentives and good returns respectively, while external stakeholders (customers) get superior quality of goods.
What is TQM practice?
Therefore, TQM practices are designed to bring in continual improvement to the quality standards of a product/service. This results in a continuous revival of processes.
What are the advantages of TQM?
The advantages of total quality management (TQM) include the following: Cost reduction. When applied consistently over time, TQM can reduce costs throughout an organization, especially in the areas of scrap, rework, field service, and warranty cost reduction.
What are the benefits of TQM?
The advantages of total quality management (TQM) include the following: 1 Cost reduction. When applied consistently over time, TQM can reduce costs throughout an organization, especially in the areas of scrap, rework, field service, and warranty cost reduction. Since these cost reductions flow straight through to bottom-line profits without any additional costs being incurred, there can be a startling increase in profitability. 2 Productivity improvement. Productivity increases significantly, since employees are spending much less of their time chasing down and correcting errors. Increased productivity means more output per employee, which typically results in increased profits. 3 Customer satisfaction. Since the company has better products and services, and its interactions with customers are relatively error-free, there should be fewer customer complaints. Fewer complaints may also mean that the resources devoted to customer service can be reduced. A higher level of customer satisfaction may also lead to increased market share, as existing customers act on the company's behalf to bring in more customers. 4 Defect reduction. TQM has a strong emphasis on improving quality within a process, rather than inspecting quality into a process. This not only reduces the time needed to fix errors, but makes it less necessary to employ a team of quality assurance personnel. 5 Morale. The ongoing and proven success of TQM, and in particular the participation of employees in that success can lead to a noticeable improvement in employee morale, which in turn reduces employee turnover, and therefore reduces the cost of hiring and training new employees.
What is TQM in process?
TQM has a strong emphasis on improving quality within a process, rather than inspecting quality into a process. This not only reduces the time needed to fix errors, but makes it less necessary to employ a team of quality assurance personnel. Morale.
How does TQM work?
TQM works best in an environment where it is strongly supported by management, it is implemented by employee teams , and there is a continual focus on process improvement that prevents errors from occurring. TQM can be implemented successfully in any part of a business, such as: Accounting. Field servicing. Finance.
What is TQM in management?
There are a number of tools available to assist in a TQM effort, such as: Benchmarking. Failure analysis. Plan-do-check-act (PDCA) cycle.
What does it mean when a company has fewer complaints?
Fewer complaints may also mean that the resources devoted to customer service can be reduced. A higher level of customer satisfaction may also lead to increased market share, as existing customers act on the company's behalf to bring in more customers. Defect reduction.
Does TQM have a negative effect on costs?
However, TQM also requires a significant training period for those employees involved in it. Since the training can take people away from their regular work, this can actually have a negative short-term effect on costs. Also, since TQM tends to result in a continuing series of incremental changes, it can generate an adverse reaction from those employees who prefer the current system, or who feel that they may lose their jobs because of it.
Why is quality management important?
1. A quality management system helps leadership. Objectives of the business are important because they govern the values and strategic direction. A mistake many leadership and management teams tend to make is to oversimplify their objectives. For example, objectives focusing solely on growth, revenue or headcount.
What is quality management?
A quality management system requires top management to ensure there is a balanced array of objectives which meets the needs of all interested parties which the business's survival depends on , e.g. customers, shareholders, managers, employees and the community.
What is the second meaning of quality?
The second meaning of quality is the set of processes, policies and procedures which constitute operational planning and decision making.
What are the benefits of QMS?
QMS adoption can offer obvious benefits such as operational consistency, efficiency, improvement, and collaboration. For a comprehensive look at how QMS adoption can benefit your bottom line, we recommend 13 Bottom Line-Boosting Benefits of a Quality Management System.
What are the objectives of QMS?
Regulatory risk, compliance, and certification are critically important objectives for implementing a QMS. However, they're not the only outcomes you can expect when adopting the right quality system. In this post, you'll learn five of the most common benefits organizations in highly regulated industries enjoy with QMS adoption.
What is continuous improvement?
Continuous improvement is among the core principles of ISO 9001 and other quality management systems. ISO writes that “continual improvement should be a permanent objective of the organization.” When adopting a QMS leads to cultural change, embracing the principle of improvement can have lasting benefits to the organization such as stronger performance, strategic leadership, and staff engagement.
What is ISO 9001:2015?
QMS frameworks such as ISO 9001:2015 provide a comprehensive blueprint for customer-focused quality management based on principles for leadership, the workforce, processes, improvement, evidence-based decisions, and relationships. Research confirms that implementing a QMS such as ISO 9001 or 13485 can offer near-term benefits to adopting ...
What is QMS flexibility?
One area where QMS should encourage flexibility is the adoption of evidence-based decision making based on real-time oversight into systems and data. In practice, the concept of evidence-based decision making involves the use of data gathered through monitoring and measurement methods.
How does consistency save money?
A consistent approach to operations can save money. Business process standardization can reduce process costs by 15 percent and reduce errors by 30 percent. Operational consistency can offer other measurable benefits such as reduced process throughput times, fewer customer complaints, and superior forecasting ability.
Why is communication important in a company?
Communication and education are vital to obtaining employee buy-in to quality objectives.
Definition Total Quality Management
Total quality management (TQM) is an organized way to deal with by and large authoritative management. The focal point of the cycle is to improve the quality of an association’s output, including labour and products, through consistent improvement of inside rehearses.
ESSENTIAL ELEMENTS OF TQM
TQM can be summed up as a quality management framework for a client-centered association that includes all workers in constant improvement. It utilizes systems, information, and successful interchanges to coordinate the quality order into the way of life and exercises of the association.
Enterprises Using Total Quality Management
While TQM began in the assembling area, its standards can be applied to an assortment of enterprises. With an emphasis on long haul change over momentary objectives, it is intended to give a durable vision to foundational change.
What are the TQM benefits?
The quality division in numerous organizations is just liable for the quality of items, with its concentrate regularly restricted to the inventory network. It has no job in driving quality all through the association, yet associations have numerous chances to drive client experience past items, with client support being a great representation.
What is tqm full form and its uses?
A few organizations are under the feeling that the expense of TQM is higher than the advantages it offers. This may be valid for the organizations in a limited scope, attempting to do all that goes under TQM.
Conclusion
Total Quality Management is rehearsed by numerous business associations throughout the planet. It is a demonstrated strategy for carrying out a quality cognizant culture across every one of the vertical and level layers of the organization.
What is quality management?
Quality management is the act of overseeing different activities and tasks within an organization. Corporate Structure Corporate structure refers to the organization of different departments or business units within a company. Depending on a company’s goals and the industry.
What are the principles of quality management?
These principles are used by top management to guide an organization’s processes towards improved performance. They include: 1. Customer Focus.
How does consistency help an organization?
It helps an organization achieve greater consistency in tasks and activities that are involved in the production of products and services. It increases efficiency in processes, reduces wastage, and improves the use of time and other resources. It helps improve customer satisfaction.
What is relationship management?
Relationship management is about creating mutually beneficial relations with suppliers and retailers. Different interested parties can impact a company’s performance. The organization should manage the supply chain process well and promote the relationship between the organization and its suppliers to optimize their impact on the company’s performance. When an organization manages its relationship with interested parties well, it is more likely to achieve sustained business collaboration and success.
What is quality planning?
Quality Planning – The process of identifying the quality standards relevant to the project and deciding how to meet them. Quality Improvement – The purposeful change of a process to improve the confidence or reliability of the outcome. Quality Control – The continuing effort to uphold a process’s integrity and reliability in achieving an outcome.
How does management engage employees?
The management engages staff in creating and delivering value whether they are full-time, part-time, outsourced, or in-house. An organization should encourage the employees to constantly improve their skills and maintain consistency. This principle also involves empowering the employees, involving them in decision making and recognizing their achievements. When people are valued, they work to their best potential because it boosts their confidence and motivation. When employees are wholly involved, it makes them feel empowered and accountable for their actions.
How can an organization be enhanced?
An organization is enhanced when leaders can manage and control the inputs and the outputs of an organization, as well as the processes used to produce the outputs. 5. Continuous Improvement. Every organization should come up with an objective to be actively involved in continuous improvement.
