
How does gear reduction work on a starter?
Gear reduction can be achieved with either spur or planetary gears. Due to the way that spur gears work, starters that use them require an offset armature, which is achieved by placing the starter drive in separate gear housing.
What are the benefits of gear reduction?
The main benefit of gear reduction is that it allows for significantly smaller starters that produce an equal or greater amount of torque in comparison to much larger direct drive starters.
What is the difference between direct drive and gear reduction?
This means direct drive requires more current from the car’s battery, larger battery cables are needed and other components are designed to handle higher current. Weight – Gear reduction starters are smaller and lighter than direct drive models.
What is a planetary gear reducer and how does it work?
The gear is called an idler and its primary function is to change the direction of rotation rather than decrease the speed or increase the torque. Calculating the gear ratio in a planetary gear reducer is less intuitive as it is dependent on the number of teeth of the sun and ring gears.
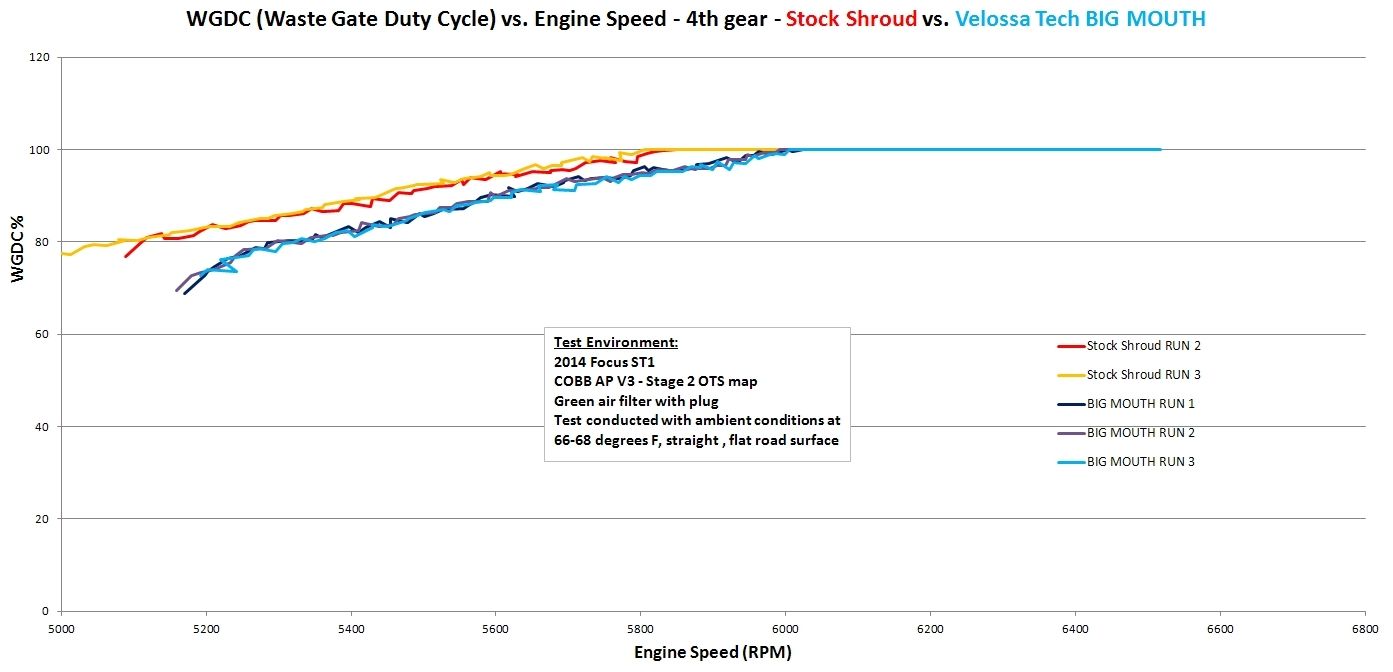
What is the purpose of gear reduction on the starter motor?
Gear reduction starters use gears to reduce the speed of a higher-speed electric motor in order to extract more torque at the flywheel end of the starter.
Why is a reduction starter sometimes used?
GEAR-REDUCTION STARTERS This permits the use of higher speed, lower current and lighter motor assembly while increasing cranking torque. The Chrysler starter made a unique, readily identifiable sound when cranking the engine.
Why does a gear reduction unit reduce the amount of current required by the starter motor?
For GM, they are direct-drive-type motors and they generate heat soak that drives the current demand up and pushes the efficiency down. By design, a gear-reduction starter is more efficient, so it requires less current draw, which causes less heat and you get more cranking power.
What is a gear reduction?
Gear Reduction or Reduction drives reduce the speed and increase torque at the output shaft. In Reduction Drive, the number of teeth on the input shaft is less than the teeth on the output shaft.
Are high torque starters worth it?
If you're going to replace a starter, "why not" go for the hi-torque unit. They're lighter, put less drain on the battery and really turn the motor over. The only caveat is, "caveat emptor".
What's the difference between a direct drive starter and a PMGR starter?
In a DD starter, components are attached in a line and run off the armature. A PLGR starter has a shaft that the armature uses and is good at increasing torque. A PMGR starter is similar to a PLGR starter except the PMGR starter uses permanent magnets instead of field coils.
Does gear reduction increase torque?
While in many applications gear reduction reduces speed and increases torque, in other applications gear reduction is used to increase speed and reduce torque.
What causes starter whine?
Freewheeling occurs when you crank the engine and simply hear a whining noise without the engine cranking. When this occurs, it means the starter is not engaging with the flywheel. This is a worrying situation which could result in having to replace the whole component.
How does gearing affect torque?
The primary purpose of the gear ratio is to reduce the torque by increasing the speed, and vice versa. Your car won't move at higher gear ratios because, at the initial stage, you need more torque than power.
Where can you use reduction gears?
Common household uses are washing machines, food blenders and window-winders. Reduction drives are also used to decrease the rotational speed of an input shaft to an appropriate output speed. Reduction drives can be a gear train design or belt driven.
What is gear reducer function?
A gear reducer increases the torque of your motor, thus allowing a receiving member to rotate under the impact of a new torque.
What are the two types of reduction gear?
There are generally two types of reduction gearboxes:Single Reduction Gearbox.Double Reduction Gearbox.
What is a reduced voltage starter?
Reduced Voltage Starter is a device that starts motors with reduced power supplied at start-up. Reducing the power reduces potentially damaging electrical and mechanical shocks on the system. As the name implies, starters "start" motors. They can also stop, reverse, accelerate and protect them.
Are direct drive and gear reduction starters interchangeable?
A gear reduction starter may appear different by design. For example, the Delco Remy 29MT™, 35MT™, 38MT™and 39MT™ all incorporate a nose-less design and don't include a cone around the starter drive. Despite this design difference, these starters are completely interchangeable with straight drive nose style starters.
What test can quickly reveal the condition of the starter motor?
STARTER PROBLEMS You can check out a customer's starter by bench testing it with the proper equipment. Using a battery and a pair of cables to jump the starter will only tell you if it spins, not how many amps it's drawing or how fast it's cranking.
Which of the following uses a small current flow from the ignition switch to control a larger current flow to the starter?
The starter relay allows a smaller current flow (from the ignition switch) to control a larger current flow (to the starter solenoid). A magnetic field is generated around a wire that carries electrical current. In a magnet, charges that are unlike will ____ each other.
Why are gear reduction starters faster?
However, because their torque is higher, they have a faster speed when pistons are at TDC on the compression stroke where it is needed most. This is why they are ideal for diesel or other high-compression engines.
What is the difference between a gear reduction starter and a direct drive starter?
Weight – Gear reduction starters are smaller and lighter than direct drive models. When replacing a direct drive starter with a gear reduction model, there is more space around it, which makes installation easier and may improve heat-resistance of the solenoid.
Why is my direct drive starter slow cranking?
Maintenance – Gear reduction starters have a higher part count, but internal wear is often less compared to direct drive starters since they use bearings versus the bushings common in direct drive starters. Misaligned or worn bushings are the most common cause of slow cranking of hot engines that use direct drive starters.
What is gear reduction?
Gear reduction starters use gears to reduce the speed of a higher-speed electric motor in order to extract more torque at the flywheel end of the starter. Two typical designs are Offset Gear Reduction and Planetary Gear Reduction.
How much power does a direct drive starter need?
Power – Direct drive starters require up to 50 percent more electrical power to turn over the car’s engine than do gear reduction starters. This means direct drive requires more current from the car’s battery, larger battery cables are needed and other components are designed to handle higher current. Weight – Gear reduction starters are smaller ...
What happens when a starter motor fails?
When a vehicle’s starter motor begins to fail, a heavy strain is placed on your vehicle’s battery and other components in the starter circuit. Repairing or replacing your starter motor at the first signs of failure saves you the added cost of replacing supporting components.
Do direct drive starters have gear reduction?
Nowadays, you often have a choice since existing direct drive starters usually have a gear reduction replacement. There are advantages and disadvantages to each design. Understanding the differences ensures you will choose the correct starter for your vehicle. Direct drive starter motors have a straightforward design.
What is the benefit of gear reduction?
The main benefit of gear reduction is that it allows for significantly smaller starters that produce an equal or greater amount of torque in comparison to much larger direct drive starters. The main drawback is that they are typically more expensive.
What is the difference between direct drive and gear reduction starters?
When direct drive and gear reduction starters are compared, direct drive units are typically cheaper , and gear reduction units tend to be smaller, lighter, ...
Why Replace Direct Drive With Gear Reduction?
Since the late 1980s, the OEMs have steadily moved away from direct drive starters toward gear reduction starters. Although gear reduction starters are more complex, which makes them more expensive, they are also smaller, lighter, and more efficient.
Why Use Direct Drive?
Although gear reduction starters are superior to direct drive in most cases, there are still a few reasons to use direct drive. The most obvious benefit of direct drive is price, which can become a rather large issue. For instance, direct drive starters are often the better choice for heavy duty diesel applications. In some of these applications, a gear reduction starter can cost 30 percent more than a direct drive unit.
What is the ratio of a starter shaft to a drive mechanism?
Although “gear reduction” technically takes place between the starter’s pinion gear and the ring gear on the flywheel or flex plate, the pinion gear itself rotates in a 1:1 ratio with the armature shaft.
How many times does the armature shaft rotate?
In either case, the armature shaft will typically rotate about four times for each rotation of the pinion gear. The main benefit of gear reduction is that it allows for significantly smaller starters that produce an equal or greater amount ...
Is gear reduction more expensive than direct drive?
These starters have also come down in price over years. So while gear reduction starters are still more expensive than direct drive starters, they are more affordable than they used to be.
What is a reduction type starter?
Abstract: A reduction type starter, wherein an idle shaft is mounted in a starter housing in parallel with a motor shaft and a pinion drive shaft, and an over running clutch is provided on the idle shaft so that a reduction of rotational speed can be performed at two stages.
What causes the increase in starter motor speed?
The gear reductions cause the increase in starter motor speed. It provides the torque multiplication that is necessary to crank an engine.
What is gear reduction?
Gear “reduction” specifically refers to the speed of the rotary machine;
How does gear reduction affect torque?
Gear reduction has the opposite effect on torque. The rotary machine’s output torque is increased by multiplying the torque by the gear ratio, less some efficiency losses. While in many applications gear reduction reduces speed and increases torque, in other applications gear reduction is used to increase speed and reduce torque.
How to find gear ratio?
The planetary gear ratio equals the sum of the number of teeth on the sun and ring gear divided by the number of teeth on the sun gear. For example, a planetary set with a 12-tooth sun gear and 72-tooth ring gear has a gear ratio of 7:1 ( [12 + 72]/12 = 7). Planetary gear sets can achieve ratios from about 3:1 to about 11:1. If more gear reduction is needed, additional planetary stages can be used.
How to determine gear reduction ratio?
The total gear reduction (ratio) is determined by multiplying each individual gear ratio from each gear set stage. If a gearbox contains 3:1, 4:1 and 5:1 gear sets, the total ratio is 60:1 (3 x 4 x 5 = 60). In our example above, the 3,450 rpm electric motor would have its speed reduced to 57.5 rpm by using a 60:1 gearbox. The 10 lb-in electric motor torque would be increased to 600 lb-in (before efficiency losses).
What is the ratio of planetary gears?
The planetary gear ratio equals the sum of the number of teeth on the sun and ring gear divided by the number of teeth on the sun gear. For example, a planetary set with a 12-tooth sun gear and 72-tooth ring gear has a gear ratio of 7:1 ( [12 + 72]/12 = 7).
What is the ratio of a pinion gear to a mating gear?
If a pinion gear and its mating gear have the same number of teeth, no reduction occurs and the gear ratio is 1:1. The gear is called an idler and its primary function is to change the direction of rotation rather than decrease the speed or increase the torque.
What is the purpose of gear reduction in wind turbines?
Generators in wind turbines use gear reduction in this manner to convert a relatively slow turbine blade speed to a high speed capable of generating electricity. These applications use gearboxes that are assembled opposite of those in applications that reduce speed and increase torque.
How does a starter motor work?
The solenoid also closes high current contacts for the starter motor, which begins to turn. Once the engine starts, the key operated switch is opened, a spring in the solenoid assembly pulls the pinion gear away from the ring gear and the starter motor stops. The starter’s pinion is clutched to its drive shift through an overrunning sparg clutch which permits the engine to transmit drive only in one direction. This is why the drive is transmitted through the pinion to the flywheel ring gear , but if the pinion remains engaged, the pinion will spin independently of its driveshift. This prevents the engine driving the starter for such backdrive would cause the starter to spin so fast as to fly apart. That is why a standard starter motor is only designed for intermittent use which would preclude its use as a generator.
How to reduce the starting current of an induction motor?
To reduce the starting current of an induction motor the voltage across the motor needs to be reduced. This can be done by autotransformer starter, star-delta starter or resistor starter. These days VVVF used extensively for speed control serves this purpose also. Whenever you start a big heavy electric motor, you need to start it slowly to prevent the rotor overheating and drowning an enormous current.
What is an electric starter?
The electric starter is a permanent-magnet or a series parallel wound direct current electric motor with a solenoid switch mounted on it. Current from the starting battery is applied to the solenoid through a key operated switch which pushes out the drive pinion on the starter drive shaft.
What is a starter motor?
A starter motor is a high-torque motor for tuning the gear on the engine flywheel. Starter motor is also known as starting motor or a starter. The function of starter is to reduce the starting current by inititlly high resistance. In RLC series circuit resistance, inductance and capacitance are connected in series. Starter is used to protect the motor from overload. If the starter is 3ph to avoid single phasing and it is used to reduce the strating current.
What is a Chrysler starter?
The Chrysler starter made a unique, readily identifiable sound when cranking the engine. This starter formed the design basis for the offset gear reduction starters now employed by the vehicles on the road. Light aircraft engines also made extensive use of this kind of starter because of its light weight that offered an advantage to the aircraft companies.
How does compressed air work on a diesel engine?
On large diesel engines and almost all diesel generators used the prime movers of the ships will use compressed air acting directly on the cylinder head. This is not ideal for the small diesel engines as it provides too much cooling on starting. The actual compressed air is provided form a large reservoir that feeds into a header located along the engine. As soon as the air starts the valve starts opening and the compressed air is admitted and the engine will being turning as it can be used on 2-cycle or 4-cycle engines and on reversing engines. On large 2-stroke engines less than one revolution of the crank shaft is needed for starting.
When was the starter introduced?
In 1962 , Chrysler introduced a starter incorporating a geartrian between the motor and the driveshaft. Rolls Royce had introduced a conceptually similar starter in 1964 but Chrysler was the first to bring volume-production unit in the market. The motor shaft was integrally cut gear teeth forming a drive gear which mesh with a larger adjacent driven gear to provide a gear reduction. This permits the use of higher speed, lower current and lighter motor assembly while increasing cranking torque.
Why is a gear reduction starter good?
The first benefit is that it can provide more torque for an engine with high compression, significant initial timing, or just any hard-to-start engine. The second benefit is the overall size of a gear-reduction starter.
What are the downsides of factory starters?
PM: A major downside to many factory starters is a heat-soak issue. For GM, they are direct-drive-type motors and they generate heat soak that drives the current demand up and pushes the efficiency down. By design, a gear-reduction starter is more efficient, so it requires less current draw, which causes less heat and you get more cranking power.
What is the difference between Mastertorque and XS starter?
The aluminum-encased solenoid and starter motor allow heat to easily dissipate from the solenoid contacts and armature. Where the two starters differ is in the gear-reduction ratio. The Mastertorque starter uses a 3.25:1 ratio, while the XS Torque starter uses a 4.4:1 ratio that gives it more overall cranking torque. Both starters use Powermaster's unique Inficlock system that allows the starter to be rotated 360 degrees to clear most any obstacle.
How much does a GM starter weigh?
The stock starter weighs in at a hefty 21.70 pounds, while the Powermaster starter weighs just 8.85 pounds. That is a 40.8 percent weight reduction.
What is timing retard?
With some racing engines, a timing-retard device is used during start-up. In some cases, engines with an aggressive camshaft make use of valvesprings with very high spring pressure. Such valvesprings can make it more difficult to start an engine, so a high-torque starter will be of benefit.
How many amps does a starter draw?
PM: On a workbench, a starter will draw 80 to 90 amps. However, during actual start-up of an engine, a starter will draw 250 to 350 amps.
What happens if you ground a car with a bad ground?
For example, a bad ground can cause the vehicle to incorrectly ground through the easiest path that it can findsuch as through the shifter cable. A general rule is to use a ground cable that is the same size as the positive cable. In addition, the ground cable should be mounted to a clean surface that does not have any rust, paint, or oil build-up.
