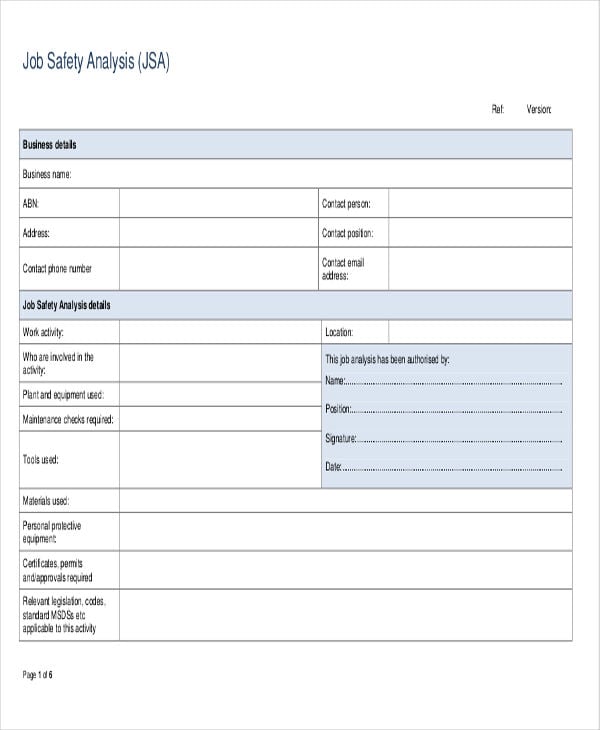
4 benefits a Job Safety Analysis (JSA) offers your company
- Meet safety standards. In addition to keeping your workers safe, complying with national safety regulations protects your company from legal and financial penalties.
- Improve communication. Completing a JSA generally requires input from multiple levels of your team. For example, safety professionals in conjunction with supervisors often create the initial JSA.
- JSA Forms Teach New Employees. When you hire a new worker, you need to onboard the person as efficiently as possible. ...
- Prevent hazardous conditions. Ultimately, the largest benefit of a JSA is also its purpose: to prevent accidents in the workplace.
What is a job safety analysis and why is it important?
Completing a Job Safety Analysis ensures that your business is meeting the standards that OSHA has laid out for the workforce. Completing a JSA helps creates visual teaching aids. Since humans are so visual this is a great tool to have for new employees when they are going through training.
Why is it important to have a job Safety Act?
Although many workers are killed or injured every day in the United States establishing proper job procedures will prevent not only injuries but also illnesses. The JSA has to also be available for workers to easily access to make sure they know the hazards associated with their jobs.
What are the benefits of hazard analysis in the workplace?
The analysis process may identify previously undetected hazards and increase the job knowledge of those participating. Safety and health awareness is raised, communication between workers and supervisors is improved, and acceptance of safe work procedures is promoted.
How to make job and safety improvements in the workplace?
The worker's experience contributes in making job and safety improvements. The job should be observed during normal times and situations. For example, if a job is routinely done only at night, the JSA review should also be done at night. Similarly, only regular tools and equipment should be used.

What are the four steps of job safety analysis?
A Breakdown of the 4 Steps of a Job Safety Analysis (JSA)Choose a job to analyze. At some point you would ideally do a JSA for every job performed in your workplace. ... Break the job down into specific tasks. ... Determine hazards and risk present in each task. ... Identify preventative controls and residual risk.
What are some of the benefits associated with a successful job safety analysis program quizlet?
what are some benefits associated with a successful JSA program?... selecting the job to be analyzed. defining the basic job steps for each task. identifying potential hazards for each step defined. developing approaches to eliminate or control identified hazards. record personal information on each employee.
What is the purpose of a safety analysis?
A job safety analysis (JSA) is a procedure which helps integrate accepted safety and health principles and practices into a particular task or job operation. In a JSA, each basic step of the job is to identify potential hazards and to recommend the safest way to do the job.
What are the 5 steps of a job hazard analysis?
Five Steps to Successful Job Safety AnalysisStep One: Choose a Job to Analyze. ... Step Two: Identify Job Site Needs and Task Breakdown. ... Step Three: Determine Hazards and Risks. ... Step Four: Develop Preventative Controls. ... Step Five: Document and Share Job Hazard Analysis Reports.
What are some of the benefits associated with a successful job analysis program?
They can help you meet safety standards, improve communication, aid in training, and prevent hazardous conditions. According to the U.S. Department of Labor, 5,147 workers were killed on the job in 2017.
What is a benefit for having a safety and health program?
Safety and health programs help businesses: Prevent workplace injuries and illnesses. Improve compliance with laws and regulations. Reduce costs, including significant reductions in workers' compensation premiums.
What are the benefits of job hazard analysis?
The many benefits of Job Hazard Analysis include: Set performance standards. Standardize operations based on acceptable safe practices and Personal Protective Equipment (PPE) Provides a form of training documentation regarding the employee's knowledge of the job requirements.
What are your goals in a job safety analysis workplace hazards identification?
The goal of a safety analysis is to look at the relationship between the work environment, the tools or equipment, the worker, and the task. Any findings should be used to implement best practices and improve the safety of the workplace.
What is the importance of a job safety analysis JSA on a construction site?
Job Safety Analysis (JSA) is a safety management tool in which the risks or hazards of a specific job in the workplace are identified, and then measures to eliminate or control those hazards are determined and implemented.
What are the 3 general phases of a JHA?
Steps of the JHA ProcessStep 1: Begin the JHA for a specific job by breaking the job down into the steps or tasks performed while doing the job. ... Step 2: Identify and list the hazards associated with each task (do one task first, then another, etc.) ... Step 3: Write a hazard description (also called a hazard scenario)More items...
What is a job safety analysis form?
A Job Safety Analysis (JSA) is a method that can be used to identify, analyze, and record 1) the steps involved in performing a specific job, 2) the existing or potential safety and health hazards associated with each step, and 3) the recommended action(s)/procedure(s) that will eliminate or reduce these hazards and ...
What are the safety issues in the workplace?
These include minor incidents like tripping and falling, to major incidents like electrocution, natural catastrophe, fire, and workplace violence, which is not restricted to physical assault but also sexual and verbal harassment or bullying.
What are the benefits of JSA?
Benefits. In the workplace, many employees are at risk. Even minor injuries can lead to serious physical injuries, trauma, and death. This is common in companies that are involved in tasks which require employees to work using heavy mechanism, tools, and equipment. The JSA helps minimize these risks.
Why is JSA important?
The JSA is beneficial to the company as well in a way that this lessens the illness or absenteeism rate, which is one of the reasons for the company’s low level of productivity and success. Without injuries and illnesses, the company has fewer instances of dealing with legal claims and lack of workforce. Safety issues in the workplace are ...
What is the role of safety department?
The safety department is able to train and educate the company’s employees about the issue and at the same provide proper safety gears. There are institutions that help assess a workplace safety program, one of which is OSHA (Occupational Safety and Health Administration).
What is the purpose of JSA?
The Benefits Of Job Safety Analysis. Job safety analysis (JSA) is a very valuable part of the workplace safety program. This helps identify and control safety hazards that are associate with the nature of the work. It is also known as job hazard analysis or JHA, risk assessment or RA, and activity hazard analysis or AHA.
How to identify workplace hazards?
In order to identify workplace hazards, the company must be able to know what may go wrong and what the possible consequences of the incident are. It is important to establish or re-establish a workplace scenario that will help determine how hazards take place, what the contributing factors are, and the chances of encountering such danger. ...
Should a company involve its employees in the job safety analysis process?
Under the regulations set by OSHA, it is indicated that: The company should involve its employees in the job safety analysis process, as every voice will be heard and this will leave no stones unturned.
Why do we use job safety analysis?
Using the findings from the job safety analysis to eliminate and/or prevent potential hazards in the workplace is a morale booster for the entire company.
Why do companies need JSA?
Having a JSA done for every position within a company makes training a new employee much easier because there is a clear system in place. This in turn also increases a new employees job performance because they are thoroughly trained right from the start when it comes to safety in their new position.
What is JSA in a job?
The JSA is a great method to clearly outline now only safe work possesses but also do it efficiently. Every job within a company will benefit from completing a JSA. Completing the JSA itself is not extremely complicated but understanding the job that is being subjected to the Job Safety Analysis is important. ...
Why is it important to comply with OSHA regulations?
It is important to comply with safety regulations in order to protect your company from any legal penalties. One of the most frequent standard violations OSHA reports is Hazard communication. Completing a Job Safety Analysis ensures that your business is meeting the standards that OSHA has laid out for the workforce.
Why do we need a JSA?
Completing a JSA helps creates visual teaching aids. Since humans are so visual this is a great tool to have for new employees when they are going through training. It is also helpful for current employees that need a refresher with an exact breakdown of the steps that are required for a specific job.
Why is OSHA important?
1) Prevents Hazardous Conditions. This is also its main purpose; preventing accidents. OSHA gives a good starting place but the regulations they set in place don’t address every single potential hazard for your business. Preventing accidents is good for both your employees and your business.
How to deal with potential hazards?
The most effective way to deal with the potential hazard is completing eliminating it by either: Choosing a different process. Changing equipment to complete the job. Substituting with less hazardous equipment. 2) Containing. When eliminating the hazard is not an option containing the hazard might be best.
How to conduct a JSA?
Conducting a JSA, the center says, can be done in four basic steps: Select the job. When deciding which jobs to perform a JSA on, consider a number of factors, including incident frequency and severity, the potential for serious injuries when performing the job , and how newly established a job is. Newer jobs may result in more injuries because ...
What is a JSA?
When a JSA is conducted , every basic step of a job is analyzed to identify potential hazards.
Why do newer jobs cause more injuries?
Newer jobs may result in more injuries because of inexperience. Additionally, CCOHS points out that infrequently performed jobs may pose greater risks because workers may not be as skilled at doing them. Break the job into steps.
How many steps should a job be described in?
Break the job into steps. Most jobs can be described in fewer than 10 steps (if not, consider breaking the job into two separate JSAs). These steps should be listed in sequential order. Have an immediate supervisor observe the task being performed under regular conditions.
What are the benefits of developing a JSA?
The analysis process may identify previously undetected hazards and increase the job knowledge of those participating . Safety and health awareness is raised, communication between workers and supervisors is improved, and acceptance of safe work procedures is promoted.
What is JSA in the workplace?
A JSA, or better still, a written work procedure based on it, can form the basis for regular contact between supervisors and workers. It can serve as a teaching aid for initial job training and as a briefing guide for infrequent jobs. It may be used as a standard for health and safety inspections or observations.
How to conduct a JSA?
Four basic stages in conducting a JSA are: 1 selecting the job to be analyzed 2 breaking the job down into a sequence of steps 3 identifying potential hazards 4 determining preventive measures to overcome these hazards
What is side by side format in JSA?
Once the analysis is completed, the results must be communicated to all workers who are, or will be, performing that job. The side-by-side format used in JSA worksheets is not an ideal one for instructional purposes. Better results can be achieved by using a narrative-style communication format.
How many steps are needed to describe a job?
A rule of thumb is that most jobs can be described in less than ten steps. If more steps are required, you might want to divide the job into two segments, each with its separate JSA, or combine steps where appropriate. As an example, the job of changing a flat tire will be used in this document.
What is a job step?
A job step is defined as a segment of the operation necessary to advance the work. See examples below. Care must be taken not to make the steps too general. Missing specific steps and their associated hazards will not help. On the other hand, if they are too detailed, there will be too many steps.
What is a JSA?
What is a Job Safety Analysis? A job safety analysis (JSA) is a procedure which helps integrate accepted safety and health principles and practices into a particular task or job operation. In a JSA, each basic step of the job is to identify potential hazards and to recommend the safest way to do the job.
Breakdown of the job safety analysis
Before conducting JSA, appropriate training is necessary to understand the task’s competency and the risk associated with the assessment. Once the supervisor has the necessary knowledge and training, job safety analysis (JSA) can be carried out in five steps
OSHA information on job safety analysis
The basic principle of JSA is to break down the work into individual tasks and analyze each task for potential safety risks or hazards. Hearing protection, fall protection, and other special types of personal protective equipment are covered under other sections of OSHA standards.
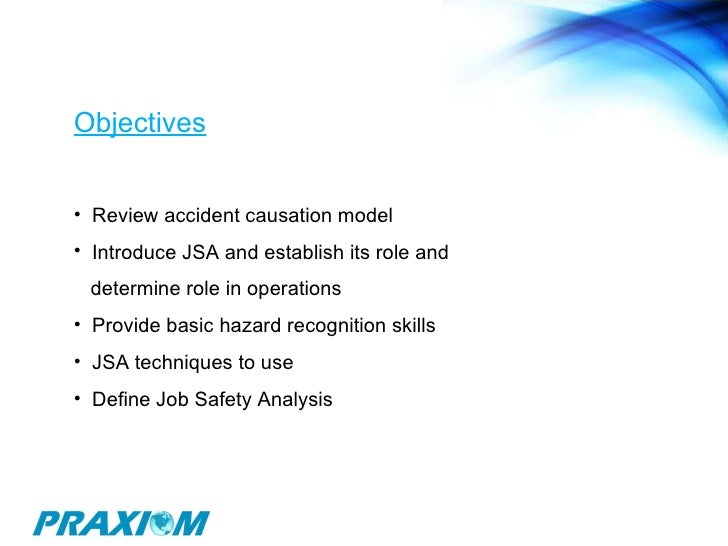